The content of the website is for reference only, please refer to the official confirmation of LEADFRP.
If you think there is something wrong with the content or Media on the websites, please contact us.
Our advanced composite FRP Box Beam suitable for major load bearing structural applications. The modular construction system consists of a small number of interlocking fiber reinforced polymer (FRP) structural components produced by the pultrusion process. The main building panels are 3.15″ (80mm) thick and either 23.68″ or 13.70″ (601.5mm or 348.0mm) wide and feature a cellular construction. Through the use of toggles and/or hangers, panels can be connected to one another, to 3-way connectors, or to 45 degree connectors.
This uniquely designed system of interlocking components makes it possible to design fiberglass structures at significantly lower costs for a broad range of construction applications. structures can be designed to be shipped flat to the job site.
Our system of five interlocking components manufactured of pultruded fiberglass reinforced polymer. The system combines manufacturing simplicity with an almost unlimited number of configurations. The panel features integral grooves into which a toggle is inserted during assembly. 3-way and 45 degree connectors allow the system components to turn corners and facilitate the joining of walls or sides. For added flexibility, the system also includes a hanger and an end cap. Joints between panels and connectors are bonded during final assembly. Adhesive is applied along the length of the panel and connector. The toggle, to which adhesive is not applied, is then inserted as an assembly aid to mechanically secure the components and create even pressure along the length of the joint until the adhesive between the structural components cures.
The pultruded fiberglass skin is available in either a premium polyester or a vinyl ester resin. Both resin systems provide flame retardance (UL 94 V-0). Vinyl ester is utilized in extreme corrosive applications. A synthetic surfacing veil is incorporated into the skin to improve weathering, corrosion resistance, and resistance to degradation from ultraviolet rays. Resistance to weathering can be further enhanced by the application of a polyurethane paint. The core material, which provides the insulation value, is a rigid closed-cell urethane foam. The ends of the panels must be encapsulated or coated with a resin similar to the skin resin to maintain the corrosion and weather resistant qualities of the total panel
FRP Box Beam Applications:
- Buildings
- Bridge Enclosure Systems
- Pedestrian Bridge Decks
- Tank Covers
- Platforms & Walkways
- Cellular Enclosures
- Secondary Containment
- Baffles
FRP Box Beam Features:
- Integral Insulation
- Lightweight
- Corrosion Resistant
- Low in Conductivity
- High Strength
- Flame Retardant
- Transparent to Electromagnetic Emissions
Size in stock (can be customized if not in the list):
All our current FRP Box Beam are customer-specific molds. You can send us your ideas or drawings for improvement.
FRP vs Traditional Materials
Traditional panel have their place. But for harsh, corrosive environments, FRP is a smart choice. Here’s how FRP compares to several traditional options
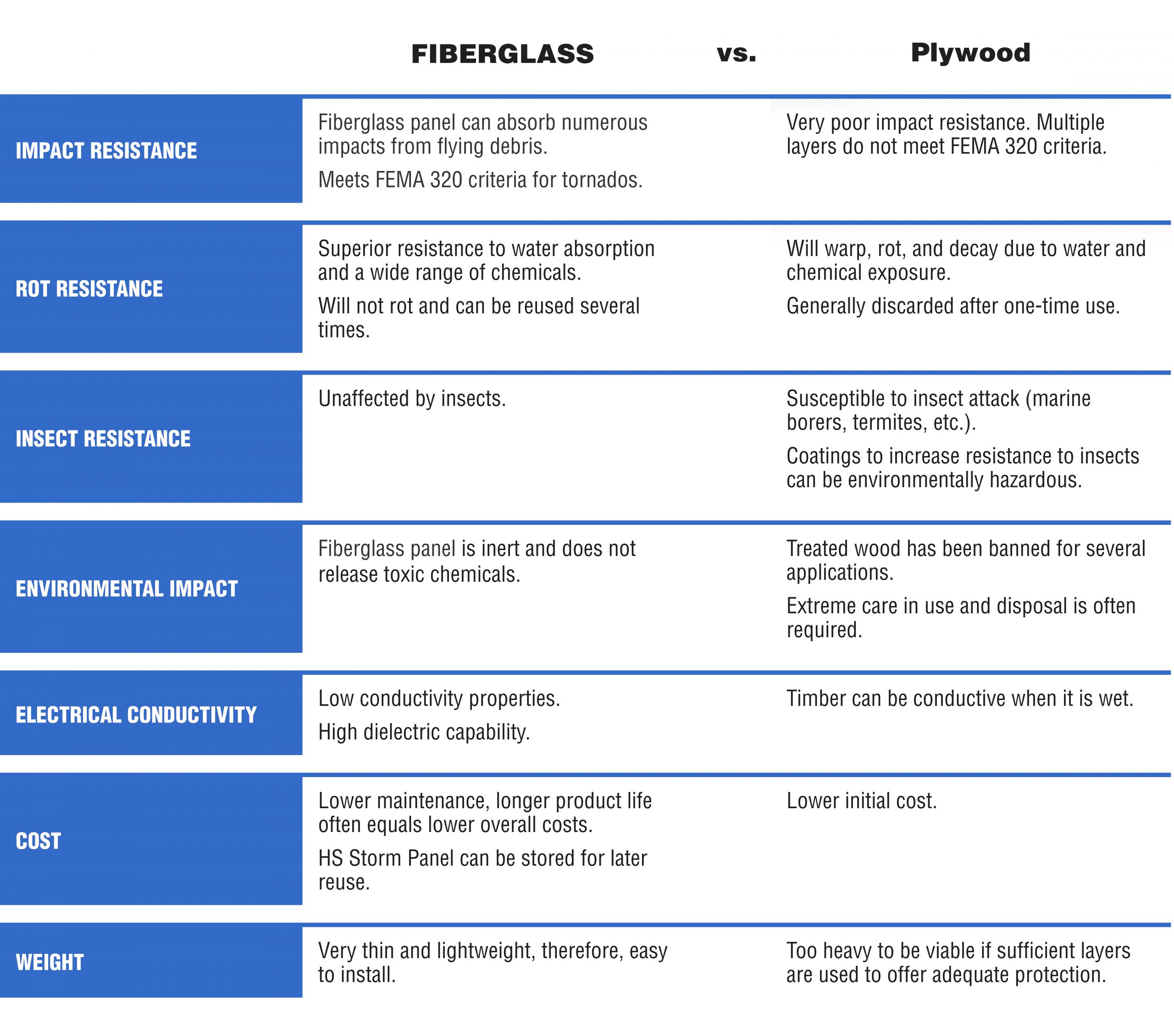
Factory Tour

At LEADFRP, we believe that fiber reinforced plastic (FRP) products are the choice of the future. Compared with traditional materials such as steel and aluminum, it has excellent performance and service life.
LEADFRP provides a series of high-strength fiber reinforced plastic products (FRP), which are designed and manufactured to provide long-lasting performance in highly corrosive environments, while having the advantages of light weight and high dielectric strength compared with traditional structural materials.
Since 2001, we have provided our customers with innovative, high-quality composite designs and materials through two strategic offices/factories located in the United States and China. It is here that we provide turnkey solutions to take your product from concept to design, to mold calculation, manufacturing, and finally to installation. [More about manufacturing]

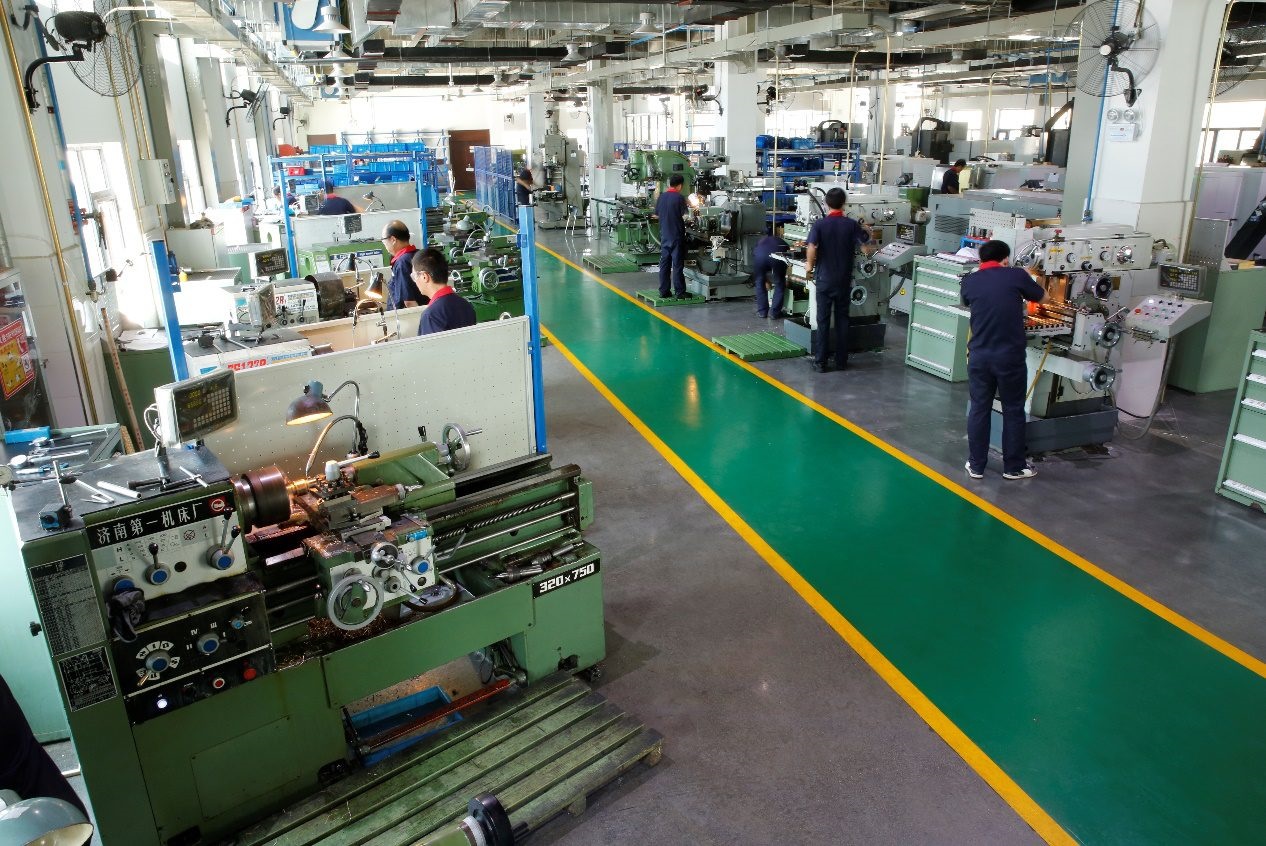
We own 5 acres (20000 square metre) standard plants, 80 sets of advanced various manufacturing and machining equipments, 120 sets of assembly pultrusion production line, including one 1000 kN tensile strength machine and one 200 kN bending and torsion machine. We also can proceed basic property test of different kinds of composite insulation materials according to GB, ASTM, etc standards. Our products passed TUV Rheinland type test and UL type test.
LEADFRP strictly carry out standardized, scientific and normalized management mode. We fully implement ISO9001 quality management system, ERP managing system and 6S management mode through the whole service cycle of contract signing, production, process inspection, finished product ex-factory, after-sales service, which outstandingly reflect ‘Quality is the Life of Enterprise’. We have ISO9001, ISO14001 and ISO45001 identification.
Technology in LEADFRP
Production Process:
Pultrusion, all Moulding type, Laminating, Casting Forming.
Feature Classification:
Food Grade, Flame Retardant, Conductive Type, anti-Corrosion, High Strength, Specific Surface.
Resin Types:
Epoxy, Polyester, Phenolic, Polyurethane, Acrylic, Polystyrene, Polypropylene, Polyethylene.
Fiber Type:
Carbon, E-Glass, ECR Glass, AR-Glass,Tow, Veil mats, Woven fabrics, Chopped strand mat.
Surface Avaliabe:
Glassfiber, Polyester, Special Type
Colors Avaliabe:
We recommend referring to RAL color standard
Size Avaliabe:
Customize Supported
Research and Development
With a 10,000 sqft R&D laboratory and full-time R&D staff, LEADFRP can perform most testing procedures, material qualifications and quality experiments. These resources provide LEADFRP, its customers and suppliers technical expertise that is unmatched in the composite industry. The following is a summary of LEADFRP’s technical capabilities.
- Decades of experience in mechanical testing of common to exotic reinforcements.
- Deflection testing a composite crossarm.
- Composites analysis capabilities including Finite Element and Classical Laminated Plate Theory using in-house generated lamina data.
- Rapid Prototyping: In-house 3D printing capabilities offer R&D lab the ability to quickly create test fixtures and concept prototypes.
- Dedicated laboratory pultrusion machine managed and operated by a full time Research and Development Engineer and dedicated machine operator.
- Competency in conducting Design of Experiments to reduce testing time.
- Material testing machines capable of loads as high as 220,000 lbs-force.
- Full Scale Testing Machine: 3-Point Bend Test Machine capable of applying loads up to 30,000 lbs-force on 22-foot clear spans.
- Environmental Chamber for elevated temperature coupon testing.
- Weatherometer and material conditioning capabilities including programmable UV, temperature and condensation.
- Laboratory machine shop to prepare ASTM test coupons and custom test specimens.
- Custom design and testing capabilities, including custom fixture design and setup, custom laminate designs and access to our in-house machine shop to fabricate test fixtures.
- Dedicated environmentally controlled Mechanical Test Lab. Dedicated environmentally controlled Electrical Test Lab.
- Rheology/DMA to determine glass transition temperature and other viscoelastic properties of resin mixes as well as solid composites.
- Viscosity and cure (210°F gel) testing capabilities for neat resins and resin mixes.
- Color matching capabilities for resins, finished pultrusions and topcoats.